Omron’s Robotic Solutions: Thousands of Possibilities
April 14, 2023
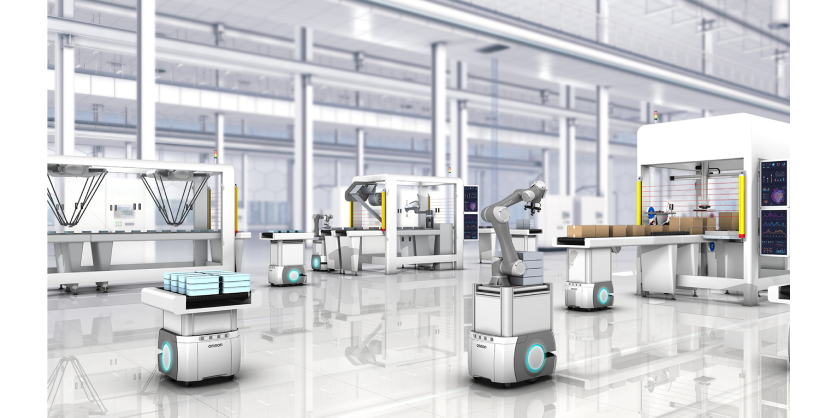
Robots can improve the productivity of many industries and processes. They can handle a variety of tasks, such as laborious or repetitive work, and can dramatically improve processes in industries such as machine tending, assembly, packaging, and other manufacturing activities. Moreover, they can handle routine operations, allowing employees to perform higher-value tasks.
This article will look at a selection of Omron’s robots and robotic solutions, such as autonomous robots and collaborative robots, and will explore how these products can be integrated into facilities to improve productivity. It also discusses the next evolution in factory automation: MoMa’s, or Mobile Manipulators – the growing trend of having collaborative robots mounted onto AMRs to achieve new levels of automation.
AGVs vs. AMRs
Autonomous robots such as AGVs (autonomous guided vehicles) and AMRs (autonomous mobile robots) can perform many of the same tasks. However, there is one fundamental difference between them. AGVs require a predefined path to follow, either a network of magnetic lines on the floor or beacons on the walls. Although AGVs allow modifications to production lines, facilities will need to install new equipment every time the AGV path is changed, leading to downtime and extra costs.
Unlike AGVs, which will stop at obstacles indefinitely, AMRs avoid stationary or moving obstacles and automatically reroute themselves when necessary. AMR paths change automatically without human intervention, which makes operations more flexible and decreases total cost of ownership. AMRs can safely navigate without the use of floor magnets or wall-mounted beacons. An AMR will first create a baseline map of a facility using built-in-sensors, then it will be capable of detecting its surroundings. When processes change, AMRs can easily change as well, creating networks of new routes or being assigned to new tasks.
Omron has developed advanced software that enables users to configure AMRs to be highly flexible in their operations that go beyond simply providing autonomous navigation, especially in applications where multiple robots are being used in “Fleets.” This allows for the most efficient workflow and the most optimal use of the AMR Fleet.
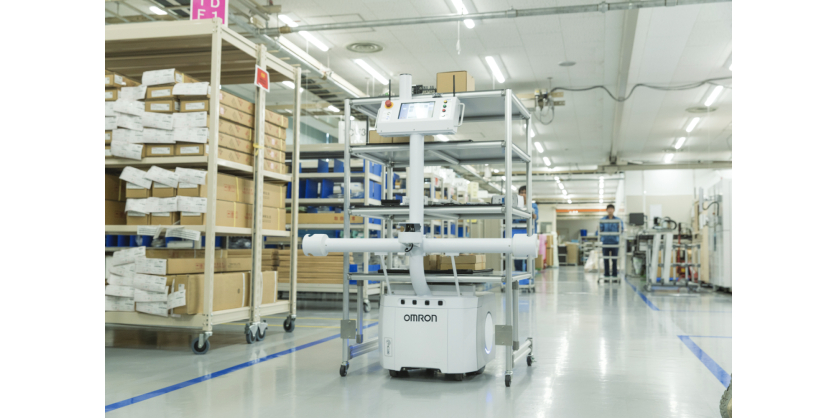
AMRs can have “personalities” defined/assigned, so that the system can differentiate between AMRs and send only the “appropriate” units to do a certain job. In addition, AMRs can determine when they need to charge based on the need of the application (i.e., the total work required to complete the assigned task), not just based on the charge level at the time.
Also, AMRs can assess the trajectory of moving objects (i.e., people, other vehicles, etc.) and intelligently yield, or fall in behind them naturally, instead of creating a potential collision situation. Furthermore, AMR routes do not need to be programmed. Instead, the AMR determines the best route to take to reach a destination and does this in the most optimal and efficient way.
As an added advantage, Omron’s AMRs have a function that is called “selectable autonomy,” wherein they can activate “AGV Mode.” This would be used when an application requires predicable motion, in a particular area. It also makes it easier to integrate AMRs into facilities with existing AGVs in use.
Collaborative Robots
Collaborative robots, or cobots, are known for being able to safely share workspaces with humans. Cobots are typically designed with beginner-friendly programming environments allowing inexperienced users to design simple applications or allowing end-users to quickly reconfigure cobots for different applications as needed. In addition, collaborative robots often have “plug-and-play” accessory ecosystems that allow users to easily add application accessories with little-to-no additional programming required.
Omron’s TM Collaborative Robots are designed for a wide variety of applications in several industries. They are well suited for assembly, palletizing, packaging, machine tending, pick and place with inspection, and screw driving. In short, they are designed for flexible manufacturing, and the success stories from customers highlight some of the ways that they have improved the processes in many industries.
Thanks to the reduced need for safeguarding, cobots can potentially be installed in existing operations with minimal needs to reconfigure a workspace. While sharing a workspace, cobots can be assigned to low-value, repetitive tasks so that humans can focus on tasks that require their talents. With graphical programming, hand guidance, and intelligent vision, Omron cobots are designed to be easy and intuitive.
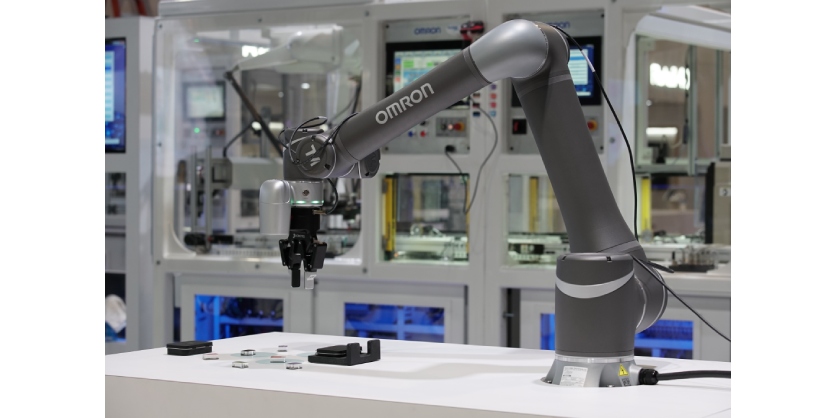
Controlling the Robotic Systems
When using an Omron NJ501-Rxxx Series Machine Automation Controller (also referred to as the Omron Integrated controller), users can connect, program, and control all the key automation technologies (i.e., robotics, motion, logic, safety, I/O, vision, etc.,) in an entire work cell on a single controller that runs on a single program. Not only does having all devices on a single platform reduce setup and programming complexity, but it also provides exceptional performance compared to solutions that require devices to be networked together.
A Gigabit EtherCAT network is dedicated for mission critical “control” communication between devices like robots, servo drives, and vision systems that enable real-time deterministic communications between devices. This results in the system’s ability to coordinate motion and operations with extremely high-performance results.
The Next Evolution in Factory Automation
Autonomous Mobile Robots or AMRs can have collaborative robots mounted on them and are sometimes referred to as “MoMa’s” or Mobile Manipulators. Still a relatively new concept, but one that is gaining traction and popularity. The next evolution in factory automation. This arrangement addresses the longstanding challenge of traditional “fixed” robots – being that they can be extremely difficult or even impossible to move automation from point A to point B once installed. It also brings many industries one step closer to addressing additional manual operations.
There are many industries and applications where a machine needs to be loaded periodically, but not with the frequency to justify dedicating a robot to sit idle during a long cycle time. In this situation, deploying a MoMa allows the robot to service the machine when it is needed, and move on to another machine or process that requires loading or unloading. The benefits here are twofold: it presents opportunities for more operations to become automated and it results in a more flexible operation overall, one that costs less compared to one where robots are fixed in place.
Interested in learning more about Omron’s robotic solutions?
Visit their Robotics Page to learn more or contact an expert today.