Q&A With HELU: Conveyor System Cables
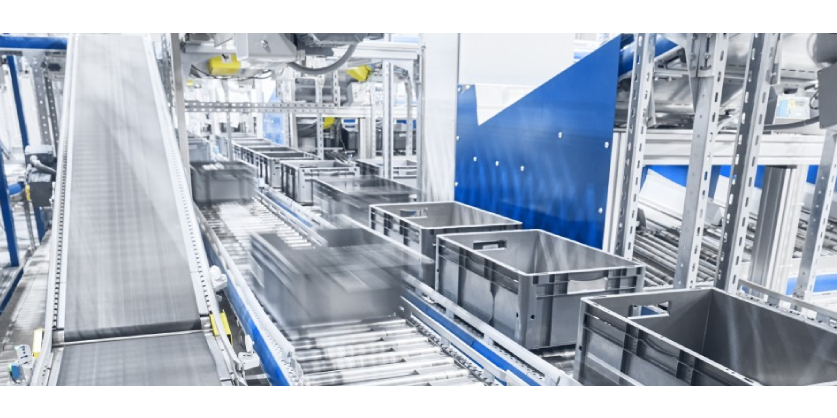
April 18, 2023
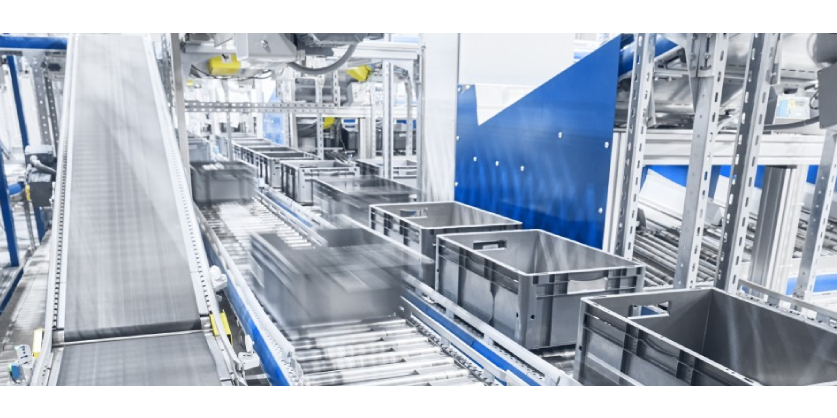
Modern conveyors are integral systems in moving products from location to location within manufacturing plants, warehouses and distribution centers around the world. Not only must they be supplied with power to keep the belts and rollers moving, but also data/communication for sub-systems that include such items as RFID scanners and vision systems in order for goods to properly navigate the extensive conveyor network. Regional Sales Director Ralf Jung discusses some of the challenges and considerations that need to be considered regarding the electrical aspects of these complex material handling systems.
Q: What common cable types are typically required by a conveyor system?
A: The most common cable types that one would find are control, power and data as well as VFD cables. Cable selection is critical given the various industrial conveyor applications and their differing electrical requirements and unique space restrictions. Typically cable specifiers need to consider the type of drive/motor in use, the available space and the types of materials being transported. Furthermore, specific sensors, which can be photo or proximity, will require the appropriate cable types.
Q: Why is cable flexibility necessary?
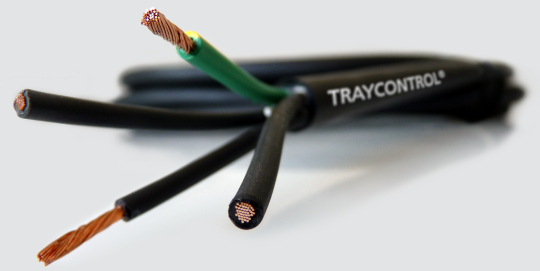
A: As previously discussed, space restrictions are typical in modern conveyor designs, especially when pre-existing structures are being renovated into warehouses and the building’s footprint is unable to be expanded. A flexible cable is advantageous during facility installations, which are typically long runs and have ample space, but it is even more critical when the installation is on a compact machine and the spacing is much tighter.
Cables constructed with Class K stranding or better offer a bend radius of 4-7.5 times the cable’s outer diameter that is typically required to ensure proper operation of the VFD, motor and sensors within a narrow space envelope in compact machines or tight areas in the facility’s overall cable network. Typical Class B-stranded cable is stiffer and tends to have a greater bend radius to avoid breaking the conductor(s), especially when larger gauge cable is used.
Q: What approvals/certifications are important to consider?
A: International machine/conveyor manufacturers design and build systems for worldwide use. Each region or country has its own electrical insulation requirements and the cables need to meet or exceed the requirements of each country. Approvals such as UL, CSA, and CE as well as HAR standards are necessary for cables of all types. Additional approvals that are important and must be considered pertain to fire/smoke regulations such as UL VW-1, CSA FT1 or FT4, and VDE 0482-332-1-2. In some cases, halogen-free cables might also be a consideration. The challenge is finding cables that have multiple approvals to simplify part lists and reduce overall inventory at the manufacturer and at the end-user’s repair facility.
Q: What effects do environmental factors have on selecting the correct cables in conveyor applications?
A: Conveyors are designed for moving a variety of products such as manufactured parts, packages, bottles, cans and food products including meats, baked goods and produce. The environment for all these types of products can range from unbearably low to extremely high temperatures, i.e. -40°C to +200°C or more, or expose the cables to harsh cleaning chemicals, such as periodic washdowns in the food and beverage space. As such, the cables and connectors selected must be specified to withstand the necessary environmental hazards of the application. This will ensure minimal downtime to keep materials moving around the facility as needed.
Q: How important is it to select the appropriate cable with respect to actual conveyor application or installation?
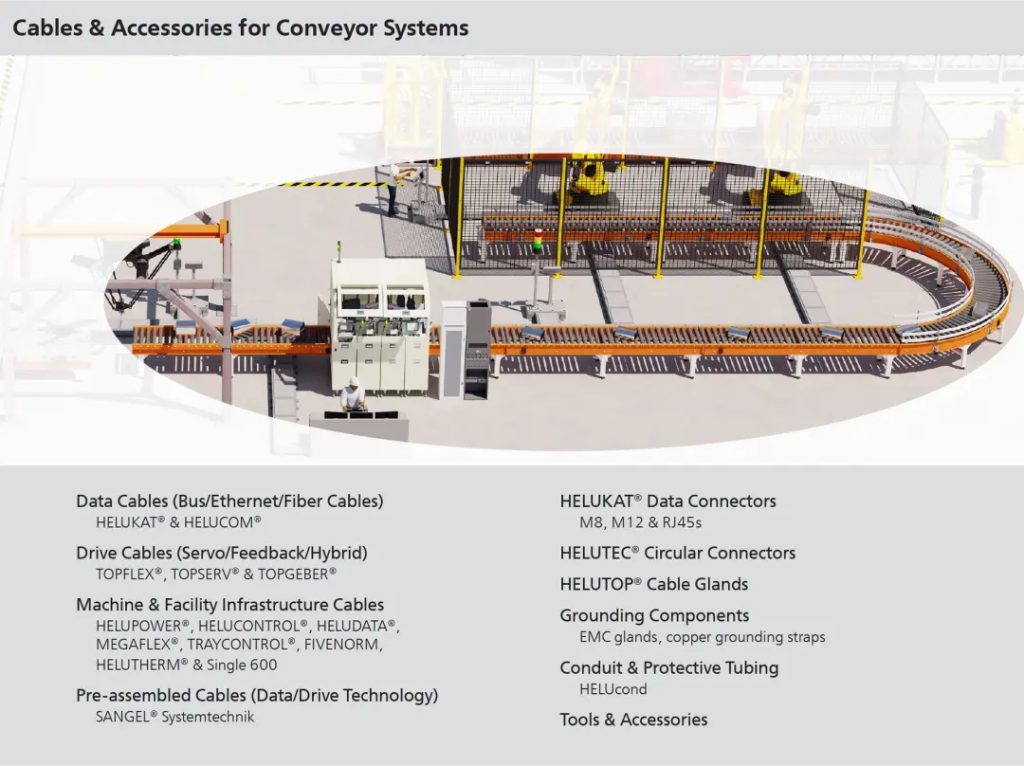
A: It is very important to know as many application and installation parameters as possible given that conveyor electrical system designs can vary – the cable is static in once place while it is flexing in another, or cables are installed in conduit while others will be exposed outside of a tray. Each parameter needs to be evaluated to ensure that the right cable or cables are selected.
For example, cables that are exposed outside of a tray or conduit, which not only routes but protects the cable, must be constructed using the proper insulation and jacket compounds to receive tray cable exposed run approval to avoid being damaged if run over by a forklift or crushed by heavy good that has fallen over. Another example would be using a cable built to withstand the complexities of a VFD motor instead of standard THHN, which causes more harm than good and usually does not meet modern industry standards. Additional considerations are for long-term service, determining whether the conveyor system and sub-systems are hard-wired or designed to be modular with connectorized cable assemblies.
While these are just some of the aspects to consider when specifying cables or cable assemblies, additional questions will most certainly arise especially for custom conveyor systems.
Related Story
HELUKABEL Group Builds New Facility for Automation Cable Solutions
The HELUKABEL Group, a global cable system solutions provider, announced it is going to build a new facility in Haan, Germany that will house its robotic dress pack and drag chain system subsidiaries under one roof. The new building will also serve as the headquarters of HELUKABEL’s Rhine-Ruhr sales branch, and is planned to be completed by 2025.